ASME MFC-22-2007 pdf free download.Measurement of Liquid by Turbine Flowmeters
6..3.9 For higher vapor pressure liquids or liquids with vapor pressures of more than 1 000 kPa or about 150 psi at the flowing conditions, it may be possible to reduce the coefficient of 1.25 in eq. (2) to some other practical and operable margin. A back pressure greater than 350 kPa or about 50 psi above the vapor pressure of the liquid for the flowing conditions is normally ade- quate for proper operation of the liquid turbine meter. In either case, the recommendations of the meter manu- facturer should be considered. During proving opera- tions, additional back pressure may be required to prevent vaporization in the prover.
6.3.10 When a flowlimiting device or a restricting orifice is required, it should be installed downstream of the meter run. A restricting orifice plate, installed downstream of the meter provides additional back pres- sure in the event of a sudden increase in flow rate due to an upset condition (generally, an increase in upstream pressure); thereby preventing the meter from operating under high flow rates that may damage the meter. An alarm may be desirable to signal a flow rate that has exceeded the design limits. Flow-limiting or other pressure-reducing devices installed upstream of the meter should be designed and located to satisfy flow- conditioning and meter pressure requirements.
6.3.11 Each meter should be installed such that neither air nor vapor can pass through it. If necessary, air and vapor elimination equipment should be installed upstream of the meter. The equipment should be installed as close to the meter as is consistent with good practice, but it must not be so close that it generates a swirl or a distorted velocity profile at the entry to the meter. Any vapor released from the line should be vented in a safe manner.
6.3.12 Meters and piping should be installed so that accidental drainage or vaporization of liquid is avoided. The piping should have no unvented high points or pockets where air or vapor could accumulate and be carried through the meter by the added turbu- lence that results from an increased flow rate. The installation should prevent air from being introduced into the system through leaky valves, piping, glands of pump shafts, separators, connecting lines, and so forth.
6.3.13 The recommended location for prover connections is downstreamofthe meterrun. Ifitis necessary to locate prover connections upstream of the meter run, it should be demonstrated that meter performance is not different between proving and normal operation.
6.3.14 Lines from the meter to the prover should be installed to minimize the possibility of air or vapor being trapped. Manual bleed valves should be installed athighpoints so thatair canbe drawnoffbefore proving. The distance between the meter and its prover should be minimized. The diameter of the connecting lines should be large enough to prevent a significant decrease in flow rate during proving. Flow rate control valves may be required downstream of each meter, particularly in multimeter installations, to keep the proving flow rate equal to the normal operating rate for each meter.
6.3.15 Piping should be designed to prevent the loss or gain of liquid between the meter and the prover during proving.
6.3.16 Special consideration should be given to the location of each meter, its accessory equipment, and the piping manifold so that mixing of dissimilar liquids is minimized.
6.3.17 Most turbine meters will register flow in both directions, but seldom with identical meter factors. If flow must be restricted to a single direction because of meter design, flow in the opposite direction should be prevented. Reverse flow can be measured by a unidi- rectional turbine meter by directing the flow through the meter always in the same direction by installing valves and piping for reverse flows.
6.3.18 A thermometer, or a thermowell that permits the use of a temperature-measuring device, should be installed in or near the inlet or outlet of a meter run so that metered stream temperatures can be determined. The device should notbe installed upstreamofthe meter between the meter and the flowconditioning sections or at a downstream location closer than the manufacturer’s recommended position. If temperature compensators are used, a suitable means of checking the operation of the compensators is required.
6.3.19 To determine meter operating pressure, a gauge, recorder, or transmitter of suitable range and accuracy should be installed near the inlet or outlet of each meter.ASME MFC-22 pdf download.ASME MFC-22-2007 pdf free download
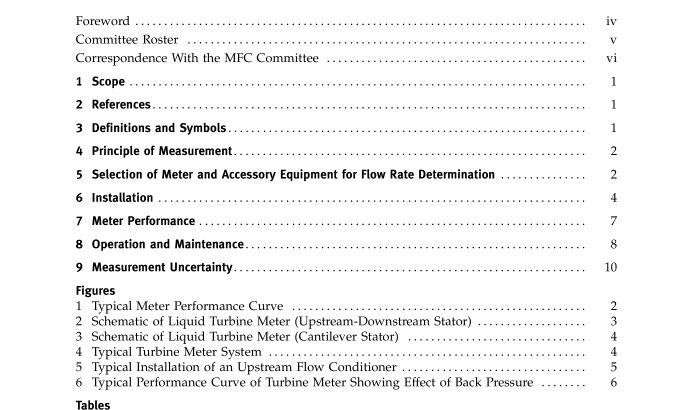