ASME MFC-16-2007 pdf free download.Measurement of Liquid Flow in Closed Conduits With Electromagnetic Flowmeters
6.2 Effects of Process Properties and Flow Profiles
6.2.1 Sizing Based on Accuracy and Velocity. The linearity of industrial electromagnetic flowmeters may be affected by the distorted velocity profile that is pres- ent at low pipe Reynolds numbers. The effect should be included in the manufacturer’s specifications.
6.2.2 Velocity Profile Effect. Pipe fittings (such as bends, valves, reducers, etc.) located upstream or downstream of the flowmeter may cause distortions in veloc- ity profile. The distorted flow patterns may influence the performance of the meter (see para. 6.4.1.1).
6.2.3 Slippage. When solids move at velocities dif- ferent from the flowing liquid, slippage occurs. In vertical installations with an upward flow direction, settling solids cancause the electromagneticflowmetertounderregister or, in extreme cases, appear as zero or reverse flow. Conversely, in vertical installations with a normallydownwardflowdirection,settlingsolids cancause the electromagnetic flowmeter to over-register. Consult the manufacturer for all slurry applications.
6.2.4 Triboelectric Effect. The triboelectric effect (static electricity) is an electrical phenomenon where materials become electrically charged due to the effects of friction. The triboelectric effect in electromagnetic flowmeters occurs when certain materials (typically nonconducting, such as silicates, petroleum-based liq- uids or solids, etc.) deposit an electrical charge (either positive or negative) on the electrodes of the meter. These charges can either introduce errors or electrical noise, or both. Consult the manufacturer when applictions include nonconductive particles.
6.3 Flowmeter Primary — Sizing Considerations
6.3.1 General Considerations. Many electromag- netic flowmeters have a relatively wide turndown, so it is generally feasible to select a flowmeter primary of the same size as the adjacent piping. However, it should be noted that liquid velocity range, upstream and down- stream piping, and other flow considerations should be the basis in choosing the meter diameter for a given application. Consideration must be given to both the maximum and minimum flow rates if the end-user requires the meter to perform as specified by the manufacturer.
6.3.1.1 Accuracy. Manufacturers must specify the meter accuracy over the liquid velocity range of the flowmeter primary. If a low velocity condition exists, it may be desirable to size the meter at less than the nomi- nal process piping size to increase the velocity (see para. 6.4.2.4). 6.3.1.2 Pipe Mismatch. Nonuniform entrance and exit conditions, such as inlet-outlet and liner internal diameter (ID) mismatches may cause changes in the velocity flow profile, which may cause additional flow 5 measurement errors. Of particular concern is the “jet effect” that occurs when the pipe immediately preceding and following the flowmeter primary has an ID less than that of the flowmeter primary (see para. 6.4.2.4).
6.3.1.3 Abrasive Slurries. Excessive wear should be a consideration for increasing the pipe diameter in the measuring section of the piping (i.e., the flowmeter sensor, and the preceding and following piping) to reduce the liquid flow velocity. NOTE: Excessive liner wear can be caused by an asymmetrical flow profile (see para. 6.2.2), improper liner material selection (see para. 6.5.2), or horizontal installation of the flowmeter primary. In particular, the upstream edge of the liner may be subject to wear from abrasive slurries. To minimize this upstream edge wear, it is beneficial to match the internal diameter of the flowmeter primary and the near upstream piping. Metal protection rings can also be installed to reduce the wear on the edge of the liner. Consult the manufacturer for guidance regarding materials of construction and installation experience for applications with abrasive slurries.
6.3.1.4 Fast-Settling Slurries. Velocities must be sufficient to keep slurry solids in suspension when the meter is mounted horizontally. Furthermore, if solids are prone to settle during no-flow conditions, there must be sufficient velocity to flush the settled materials from the flowmeter primary at startup (see para. 6.4.1.3).
6.3.2 Special Process Considerations. There may be situations where it is desirable to size the flowmeter at otherthanthepipesize. Whenthis is thecase,the process liquid properties and velocity range of the flowmeter must be considered. As a matter ofpractice, applications utilizing small meters [12 mm ( 1 ⁄ 2 in.) and less] are more sensitive to pipe mismatch effects than larger meters and should be given special consideration.ASME MFC-16 pdf download.ASME MFC-16-2007 pdf free download
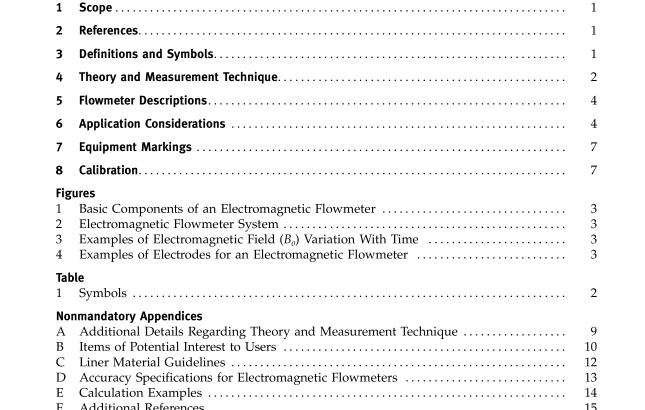