ASME MFC-8M-2001 pdf free download.FLUID FLOW IN CLOSED CONDUITS: CONNECTIONS FOR PRESSURE SIGNAL TRANSMISSIONS BETWEEN PRIMARY AND SECONDARY DEVICES
3.4 Pressure
Test An approved hydrostatic pressure test may be required for piping systems to prove the integrity of the pressure containing parts of the piping system.
3.5 Inspection A visual inspection of each installation is recom- mended for adherence to safety and measurement re- quirements before putting each flowmeter into operation (see MFC-3M). Install primary per manufacturer instruc- tions.
3.6 Rod Out Some installations will require provision for rodding out of the process connections. This is the use of a rod or other physical device to remove materials blocking the free flow of fluid into the impulse lines. Observe the applicable safety precautions.
3.7 Valve Orientation Globe style block valves may create a pocket of gas or liquid if they are installed with the stem in the vertical orientation. This pocket may result in a pressure difference and an error in the indicated measurement. Installation with the stem at an angle of 90 deg from the vertical normally solves this problem. Ball valves and gate valves do not have this problem.
3.8 Manifold Valves are often installed to permit calibrating the secondary device without removing it. These are used to block the impulse pressure lines from the primary device and to open a path between the high and low secondary device pressure taps. Where specified, two additional valves are installed to allow draining or venting of the impulse piping to the atmosphere or drain. The secondary device zero, or no flow signal, can be adjusted at operating pressure with one block valve closed and the bypass valve open. Manufactured valve manifolds may reduce cost and save space. Mani- folds integrate the required valves and connections into one assembly and have connection spacing compatible with orifice flanges and the standard secondary devices. (see Fig. C1). Install manifolds in the orientation speci- fied by the manufacturer to avoid possible errors caused by pockets of trapped gas or liquid in the body.
3.9 Installation The preferred design will minimize the separation between the primary and secondary devices. In some installations, the isolation valves and the bypass manifold are omitted. As an alternative (see Fig. 1), the bypass manifold may be installed to the back connections of the secondary to further reduce fittings and obstructions to pressure signal flow.
The connecting piping is variously referred to as impulse lines, gauge lines, instrument tubing, or instrument piping. The detail design for the installation of the flowmeter secondary system should consider instrument trouble- shooting and calibration. Access to the impulse lines, the valves, manifold and the secondary device is required. Installations providing this access must not compromise the measurement accuracy by adding excessive pressure sensing lines and fittings. Longer and more complex piping may increase uncertainties and provide more opportunity for plugging.
Plugged lines lead to loss of control and may create hazardous situations. Any difference in elevation between the primary device pressure taps and the secondary will result in a pressure difference between the two ends. If the fluids in the two lines are not identical in density, a difference in pressure is generated. Density differences will arise if there is a temperature difference between the fluids in the two impulse lines. (See Appendix B for an example of a typical calculation.) It is recom- mended that the two impulse lines are fastened together and, if insulated, they are insulated together. Nonidentical fluids in the two impulse lines can also give rise to density differences. It is also recommended that, where allowable, the secondary be “bled” or “vented” after installation to clear the impulse lines of fluids left during the construction or after hydrostatic testing or system cleaning. Bleed valves may be included in manifolds or in the secondary device body, or installed as needed. Periodic bleeding may be required if the characteristics of the fluids in the impulse lines change over time with fluid aging and with diffusion or leakage into or out of the impulse lines.
The general experience in industry is that dirt is everywhere, and that liquids will have entrained or condensed liquids. It is good practice to design the installation to allow for natural draining of liquids or venting of gases.ASME MFC-8M pdf download.ASME MFC-8M-2001 pdf free download
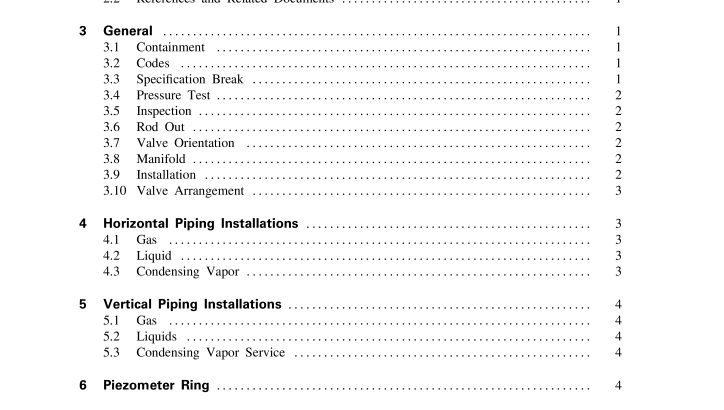