ASME B16.29-2017 pdf free download.Wrought Copper and Wrought Copper Alloy Solder-Joint Drainage Fittings — DWV
6 COMPONENT SIZE
6.1 Nominal Size As applied in this Standard, the use of the phrase “nominal size” followed by a dimensionless number is for the purpose of fitting end connection size identification.
6.1.1 Tube. The size designations for the fitting end configurations defined in Table 1 (Table I-1) correspond to drainage tube sizes defined in ASTM B306.
6.1.2 Pipe. The size designation ofthreaded fitting end configurations defined in Table 2 (Table I-2) corresponds to thread sizes defined in ASME B1.20.1.
6.2 Identification Fittings shall be identified by the nominal size of the openings in the sequence illustrated in Figure 1.
7 MARKING Each fitting shall be marked permanently and legibly with the manufacturer’s name or trademark and with DWV (to indicate drain-waste-vent).
8 MATERIAL Fittings shall be made of wrought copper or wrought copper alloy material having not less than 84% ofcopper content.
9 LAYING LENGTHS Due to widely varying manufacturing processes, laying lengthdimensionsoffittingsarenotstandardized.Consult the manufacturerforthese dimensions. Suggested dimen- sions, including laying lengths, for various fitting config- urations are shown in Tables 3 through 13 (Tables I-3 through I-13).
10 OVALITY Maximum ovality shall not exceed 1% ofthe maximum diameter shown in Table 1 (Table I-1). The average ofthe maximum and minimum diameters must be within the dimensions shown in the table.
11 THREADED ENDS
11.1 General Fittingthreads shall be righthand, conformingto ASME B1.20.1. They shall be American National Standard taper pipe threads (NPT), except for slip-joint ends, which shall have American National Standard free-fitting straight mechanical pipe threads (NPSM).
11.2 Chamfer All internal threads shall be countersunka distance not less than one-half the pitch of the thread at an angle of approximately 45 deg with the axis of the thread. All external threads shall be chamfered at an angle of 30 deg to 45 deg from the axis. Countersinking and cham- fering shall be concentric with the threads. The length of threads shall be measured to include the countersink or chamfer.
11.3 Threading Tolerances
11.3.1 Internal Threads. Variations in NPT internal threading shall be limited to one turn large or one turn small from the gaging notch when using working gages. The reference point for gaging is the starting end of the fitting, provided the chamfer does not exceed the major diameter of the internal thread. When a chamfer on the internal thread exceeds this limit, the reference point becomes the last thread scratch on the chamfer cone.
11.3.2 External Threads. Variations in NPT external threading shall be limited to one turn large or one turn small from the gage face of ring when using working gages. The reference point for gaging is the end of the thread, provided the chamfer is not smaller than the minor diameter of the external thread. When a chamfer on the external thread exceeds this limit, the reference point becomes the last thread scratch on the chamfer cone.
12 DESIGN OF THREADED ENDS External and internal threaded ends of fittings will be furnished with a polygon to facilitate installation. 13 ALIGNMENT The maximum allowable variation in the angular alignment ofall openings shall be 5 mm in 1 m (0.06 in. in 1 ft) (0.5%), other than in the direction ofpitch (see section 4).
14 GAGING 14.1 Standard Gaging Method ofSolder-JointEnds The standard method ofgagingthe diametertolerances for external and internal ends shall be byuse ofplain plug and ring gages designed to hold the product within the limits established in Table 1 (Table I-1).
14.2 Optional Gaging Method ofSolder-Joint Ends For gaging the diameter tolerance of external and internal ends, the manufacturer may use direct reading instruments instead of ring and plug gages as specified in para.
14.1. When gaging the diameters of external and internal ends using direct reading instruments, refer to section 10. In case of a dispute, ring/plug gages shall be used as the referee method.ASME B16.29 pdf download.ASME B16.29-2017 pdf free download
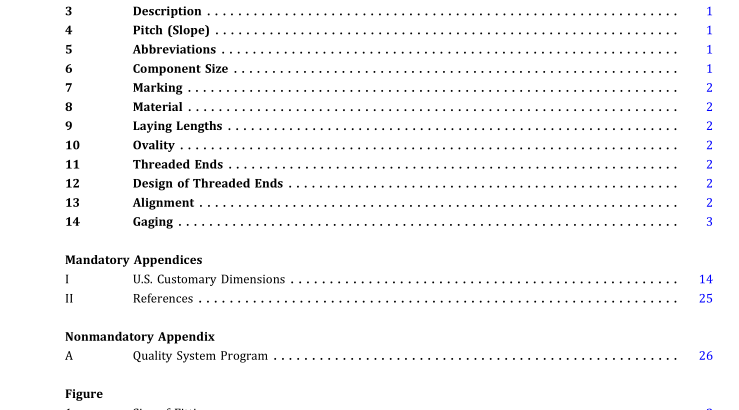