ASME A112.14.3-2000 pdf free download.GREASE INTERCEPTORS
2.4 Flow Controls and/or Vents
2.4.1 The use and placement of flow controls and/ or vents or air intakes for grease interceptors shall be the option of the manufacturer.
2.4.2 When a flow control and/or vent is used during testing for rating a grease interceptor, the rating of the unit shall not exceed the maximum flow through the flow control. The manufacturer’s literature shall reflect that the rating was achieved with the flow control and/ or vent attached, and that the flow control and/or vent shall be installed with the unit.
3 TESTING
3.1 Construction of Test Equipment
3.1.1 Test Sink. The sink used in the tests shall have the following inside dimensions: 8 ft (2.44 m) in length; 2 ft (0.60 m) in width; 12 1 ⁄ 2 in. (0.32 m) in depth. The sink shall be constructed of corrosion- resistant material and shall have two compartments, each 4 ft (1.22 m) in length. The sink shall be structurally reinforced and supported on legs. The legs shall be of proper length so that the rim of the sink will be 3 ft (0.91 m) above the floor. The sink legs shall be structurally braced. Two sinks of the above description shall be used when tests are conducted for flow rates greater than 50 gpm (190 L/m) but not exceeding 100 gpm (380 L/m).
3.1.1.1 Sink Waste Connections. Each sink compartment shall be fitted with a 1 1 ⁄ 2 in. (38 mm) standard sink waste connection with flange, crossbars, threaded or slip joint tailpiece, and locknut. The waste connections shall be located on opposite sides of the center partition in the corner formed by the side of the sink and the center partition.
3.1.1.2 Water Level Gauges. Each compart- ment shall be equipped with a gauge connection and a water level gauge with gauge glass. Each gauge connection shall be fitted into the bottom of a sink compartment and in close proximity to the waste outlet. Each gauge shall be mounted on the outside of the sink, adjacent to its respective gauge connection, and shall extend diagonally upward from the bottom center to the top outside corners. These gauges shall be calibrated to read directly the number of inches of water in the sink compartments above the sink waste flange.
3.1.1.3 Movable Sink Partitions. Each com- partment of the sink shall be fitted with a movable partition, making it possible to regulate the size of the compartment to any desired capacity.
3.1.2 Skimming Tank. The skimming tank shall be rectangular in shape; open at the top and equipped with a stationary baffle located approximately 3 ft (0.91 m) from the end of the tank receiving the discharge from the interceptor. This baffle shall extend the width of the tank and to within 4 in. (100 mm) of the bottom of the tank. The purpose of this baffle shall be to limit the heavy spread of grease to one end of the tank and to control to a degree the turbulent water currents created by the overflow from the interceptor. The dimensions of the tank shall be approximately 8 ft (2.44 m) in length, 28 in. (0.70 m) in width, and 32 in. (0.81 m) in depth. The tank shall be constructed of galvanized sheet or corrosion-resistant metal with structural reinforcement. The waste outlet from the tank shall be 4 in. (100 mm) in diameter, connected to the bottom of the tank at one end and trapped to retain approximately 26 in. (0.66 m) of water in the tank. The tank shall also be provided with a 4-in. (100 mm) valved bottom drain to permit draining and cleaning.
3.2 Installation of Testing Equipment
3.2.1 Direct Connection Test Types A, B, and C. See Figs. 1 and 2. 3.2.1.1 Waste Piping. The combined horizontal waste, vertical waste riser, interceptor inlet, and dis- charge piping shall be 2 in. (50 mm) for test flows of 50 gpm (190 L/m) or less and 3 in. (76 mm) for test flows over 50 gpm (190 L/m).
3.2.1.2 Sink and Interceptor Locations. The sink shall be located with the sink rim 13 ft (3.96 m) above the outside bottom of the grease interceptor being tested. 3.2.1.3 Skimming Tank Location. The skim- ming tank shall be located low enough, with respect to the interceptor, for the discharge piping from the interceptor to clear the tank rim by not less than 3 in. (76 mm).ASME A112.14.3 pdf download.ASME A112.14.3-2000 pdf free download
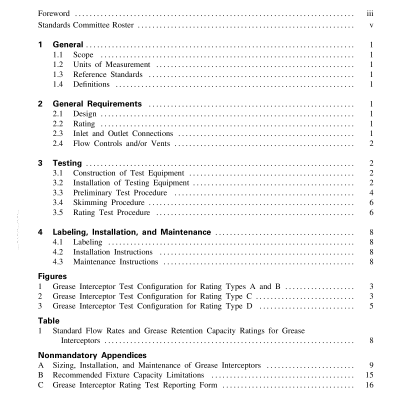