ASME A112.6.7-2001 pdf free download.ENAMELED AND EPOXY COATED CAST IRON AND PVC PLASTIC SANITARY FLOOR SINKS
2.2 Epoxy Coating The visible surface after installation of each floor sink shall be acid-resisting epoxy, thoroughly fused to the cast iron base. It shall be free from flaws that may effect the appearance or serviceability of the floor sink. The epoxy surface shall be examined for blemishes in accordance with Section 6 of ASME A112.19.1.
2.2.1 Surface Epoxy. The surface epoxy, visible after installation, shall be glossy to the extent that it will have a 1.05 rad. (60 deg.) specular gloss of not less than 60 when tested in accordance with para. 5.2.
2.2.2 Epoxy Thickness. The thickness of the ep- oxy coating, as measured on a flat surface at least 1 in. (25 mm) from any edge shall not be less than 4 mils (0.1 mm).
2.2.3 Acid Resistance. The epoxy coating shall be acid resisting when tested in accordance with para. 5.3.
2.2.4 Epoxy Flexibility. The epoxy shall be flexi- ble when tested in accordance with para. 5.4.
2.3 Detail Requirements for PVC All floor sinks plastic parts shall be of PVC material.
2.3.1 PVC Floor Sinks. All PVC floor sinks shall be made of a single PVC virgin compound except as provided in para. 2.3.2 and shall conform to the requirements specified in ASTM D 1784 for a PVC 12454 compound.
2.3.2 Reworked Plastic. Clean, reworked plastic generated from the manufacturer’s own PVC 12454 products may be used provided the floor sinks produced meet the requirements of this Standard.
2.3.3 Grates. The grates must be aligned properly and fastened by accompanying screws, unless floor sink design is for loose set installation.
2.3.4 Screws. All screws shall be made ofcorrosion resistant material.
2.3.5 Dimensions. PVC floor sink dimensions shall conform to the socket and spigot dimensions as specified in ASTM D 2665. 2.3.6 Open Area. The grates and strainers shall comply to the open area requirements of ASME A112.21.1.
2.3.7 Top Loading. Top loading classifications for grates shall be in accordance with ASME A112.21.1.
3 FLOOR SINK TYPES AND SIZES 3.1 Illustrations The floor sink type and sizes illustrated in Figs. 1 through 4 are commonly cast iron and Figs. 5 through 7 are commonly PVC, but other type materials may be provided. Those illustrated represent a selection for ordinary types and may be provided with a variey of tops. Top grates shall meet the requirements of ASME A112.21.1.
3.2 Floor Sinks Without Anchor Flanges Floor sinks without anchor flanges are for use where anchoring or clamping of a waterproof membrane is not required.
3.3 Floor Sinks With Anchor Flanges Floor sinks with anchor flanges are for use where anchoring or clamping of a waterproof membrane is required. The membrane is to be secured to the anchor flange with flange clamps. Provisions shall be made in the drain body for weepholes. They shall be cast in the cast iron body and drilled in the PVC body if necessary (see Figs. 5 through 7).
3.4 Grate Configurations Grate configurations shall be either full, 3 / 4 , or 1 / 2 design. See Figs. 8 through 10. Direction of slots may vary depending on the manufacturer.
4 OUTLET SIZE AND CONNECTION Outlet size and connections shall be in accordance with ASME A112.21.1 and/or ASTM A 888. PVC shall also be in accordance with ASTM D 2665.
5 TESTING
5.1 Enameled Cast Iron Floor Sink Enameled cast iron floor sinks shall be subjected to the tests outlined in Section 7, ASME A112.19.1, with the exception of the Lavatory Overflow Test (para. 7.5).
5.2 Specular Gloss of the Epoxy Coating The specular gloss of the epoxy shall be determined in accordance with ASTM D 523 for 1.05 rad (60 deg).
5.3 Acid Test for the Epoxy Coating The acid test for the epoxy coating shall be a fresh solution made of one (1) part citric acid crystals to ten (10) parts water by weight applied to the surface of the epoxy coating for 15 minutes, at the end of which period, after washing and drying, there shall be no loss of epoxy. The floor sink and acid solution shall have been stored for not less than 3 hr immediately preceding the test in an atmosphere of 80°F ±10°F (26.67°C ±5.55°C). The test shall be applied to a clean 3 area, in a pool of several drops and covered with a watch glass to hold the solution in place.ASME A112.6.7 pdf download.ASME A112.6.7-2001 pdf free download
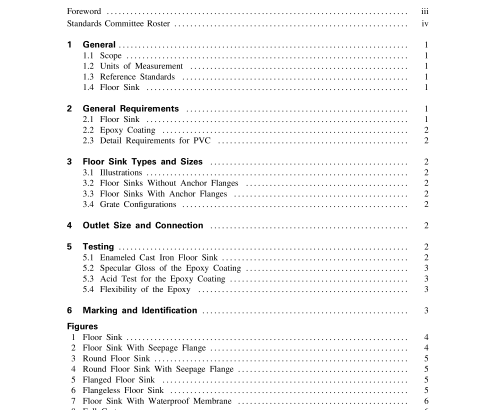